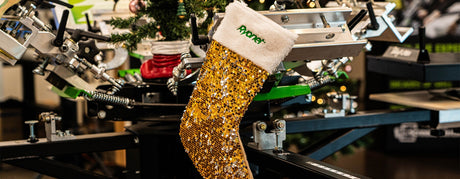
How to Embroider Fluffy Fabrics Without Losing Your Design
Have you ever embroidered on fluffy materials like stockings, Sherpa, or other plush fabrics? If so, you’ve probably seen your stitches disappear right into the fluff. Don’t worry! This guide shows you...